氢能作为热值高、无碳排、无污染的“终极能源”,推广的关键在于全产业链降本。其中,氢储运是至关重要的一环,它涉及氢气的储存、运输和配送,对氢能产业的商业化和规模化发展起着决定性作用。目前,氢气储运成本占终端用氢成本构成比例超30%。近年来,储氢瓶材料的国产替代、固态储氢的崛起等给氢储运产业带来了新的发展前景。
气液固三条储氢路线特点不同,有各自适应场景
氢气的储存方式主要有气态储氢、液态储氢和固态储氢三种形式。气态储氢技术相对成熟,主要通过高压储氢瓶实现;液态储氢和固态储氢技术尚未实现商业化,但近年来持续有技术进展,具备发展潜力。
高压气态储氢是指通过高压将氢气压缩到一个耐高压的容器或地下储气库中,其储氢量与储存压力成正比。目前应用最多的容器是储气罐和车载储氢瓶,压力通常分为35MPa和70MPa两个级别。气态储氢在当前所有储氢路线中应用最为广泛,当下制约国内高压储氢进一步发展的主要因素是储氢瓶部分材料、工艺、零部件仍然依赖进口,国产替代品性能仍有差距。
液态储氢包含低温液态储氢和有机液态储氢两种技术路线。低温液态储氢基本原理是将氢气压缩冷却至-253℃使其液化,并储存在低温绝热容器中,液氢密度可达70.78kg/m³。该技术具备储量大、纯度高、占地小、充装快等优势,但氢气液化温度低,导致液化过程能耗高,液化1kg的氢气需要耗电4-10千瓦时,且需要特殊的抗冻、抗压、高绝热储氢容器,综合成本居高不下,因此应用限制在航空等少数场景,未能拓展至民用领域。
有机液态储氢是利用氢气与有机介质发生可逆化学反应,实现氢的储存和释放。烯烃、炔烃、芳烃等不饱和液态有机物是目前较为常见的有机液态储氢材料。该技术具备稳定性高、安全性好、储氢密度大、储氢介质可循环使用等优势,但存在脱氢温度高、效率低、能耗大等问题。受制于高昂的成本,目前两条液态储氢路线仍处于研发示范阶段。
固态储氢是近年来的新亮点,分为物理吸附储氢和化学储氢两种路线。物理吸附储氢是指通过范德华力将氢气分子吸附在固体表面,储氢材料包括碳基材料、无机多孔材料和金属有机骨架化合物等,其缺点主要在于大多数物理吸附类材料在较低的温度下才能达到一定的储氢密度,常温常压下吸氢量很低。化学储氢材料主要包括金属氢化物、配位氢化物、化学氢化物等。其中,金属氢化物因其高氢储存容量和良好的循环稳定性而成为研究重点。固态储氢可在接近常温常压的环境中完成储放,兼具体积储氢密度高、可逆性、循环寿命高、安全性好、供氢纯度高等优点,应用前景为市场所看好。
中国能建(601868.SH)华北电力设计院高级工程师田江南对第一财经表示,三种储氢路线有各自适用的应用场景,没有孰优孰劣之分。他指出,氢能储运成本与储运距离和储运量有密切关系,短距离、低用量的氢气需求(运距200km以内)适合高压气态储运和固态合金储运,但前者需要用氢端投资建设高压氢气存储设施;中距离低用量的氢气需求(运距200-500km以内)适合液氢储运,但目前氢气液化成本仍然较高,另外需考虑液氢日常储存过程中产生的汽化损失;长距离高用量的氢气需求(运距大于500km)适合长输管道运输,但是氢气长输管道初始投资较高。
Ⅳ型瓶性能成本更优,但取代Ⅲ型瓶仍待时日
储氢瓶是高压气态储氢的关键载体,也是氢储运中商业化程度较高的环节。当前国内车载储氢瓶仍以35MPa的Ⅲ型瓶为主,已经批量应用;Ⅳ型储氢瓶不断取得研发进展,迎来了国家标准规范,正在加速发展,是下阶段值得关注的重点。
二者主要区别在于Ⅲ型瓶内胆材料为铝合金,Ⅳ型瓶内胆材料为高复合塑料;共同点在于外部均为全向缠绕碳纤维复合材料。与Ⅲ型储氢瓶相比,Ⅳ型储氢瓶具备更多优点:
自重轻:Ⅲ型瓶重容比约为0.98,Ⅳ型瓶重容比约为0.74,重容比越小,相同容积下储氢瓶的质量越轻,从而可以提高有效载荷;
储氢量高:Ⅳ型瓶的储氢密度在6%以上,Ⅲ型瓶的储氢密度在4%左右,储氢密度越大,同等质量的储氢瓶储存的氢气越多;
寿命长:Ⅳ型瓶的内胆是塑料材质,更不易疲劳失效,使用年限可延长至15年;
氢脆风险低:Ⅳ型储氢瓶的内胆通常采用高复合塑料,相比Ⅲ型瓶的金属内胆更耐腐蚀,可以有效避免应力腐蚀和氢脆现象。
Ⅳ型储氢瓶不仅性能更优,成本也低于Ⅲ型储氢瓶。根据中国科学院宁波材料技术与工程研究所近期的测算,35MPa、70MPa的储氢Ⅲ型瓶成本价格分别为3084美元、3921美元,而35MPa、70MPa的储氢Ⅳ型瓶成本价格分别为2865美元和3486美元,分别低7%和11%。
其主要原因有三点:
内胆材料:Ⅳ型瓶的内胆采用高复合塑料,如聚酰胺(PA)或高密度聚乙烯(HDPE),相比Ⅲ型瓶的金属铝内胆,在单位质量上的价格更低,且易于成型,从而降低了整体制造成本;
缠绕工艺:Ⅳ型瓶的塑料内胆不需要热处理,且成型更加容易,相比Ⅲ型瓶的金属内胆,其缠绕工艺更为简便,降低了制造成本;
材料节约性:碳纤维是储氢瓶成本的最主要部分,Ⅳ型瓶在设计时可以提高碳纤维复合材料利用率,减少材料的使用量,从而降低成本,随着缠绕设备的生产效率、现行设计的精准度等方面的提升,Ⅳ型瓶的成本优势将更加明显。
2023年5月23日,我国国家标准《车用压缩氢气塑料内胆碳纤维全缠绕气瓶》发布,于2024年6月1日正式实施,标志着Ⅳ型瓶的标准化向前迈进了重要一步,产业化进程有望加速。
但这并不意味着Ⅳ型瓶替代Ⅲ型瓶的进程会一蹴而就。
在今年6月的2024国际氢能与燃料电池汽车大会上,中材科技(002080.SZ)副总经理李桦圣表示,在35MPa的工作压力下,大容积Ⅲ型瓶与Ⅳ型瓶子相比更具成本优势,对于公交车、城市物流车、专用车等对轻量化和续航并不会有很高要求的车型,35MPa的Ⅲ型瓶方案基本可以满足运营需求,Ⅳ型瓶的性能优势并不明显。而在70MPa的工作压力下,Ⅳ型瓶轻量化、低成本的优势才得以凸显。重卡车型对于轻量化和续航需求就更高,大容积、高压力的Ⅳ型瓶产品在重卡领域可能也会拥有更多机会。
此外,也有业内分析指出,Ⅳ型瓶的塑料内胆与金属接头之间密封可靠性不足、塑料内胆刚度偏低、对温度更敏感的问题也有待进一步解决。
以此判断,Ⅲ型瓶和Ⅳ型瓶在未来一段时间内将形成错位竞争关系,而非完全替代。
储氢瓶厂商中,中集安瑞科(3899.HK)是能源储运设备的生产厂商和工程服务厂商,其业务覆盖整个氢能产业链,包括高压管束氢气运输车、液氢储罐、加氢机等设备的生产。公司2021年与Hexagon Purus AS合作,计划建立年产能约为10万个储氢瓶的生产线,并预计在2024年投产。
中材科技已建设完成年产10万只氢气瓶智能化缠绕生产线,并具备3万只储氢瓶产能,计划在“十四五”末期形成20万只产能。公司是国内首家既掌握70MPa IV型储氢气瓶关键核心技术、拥有自主知识产权,又同时具备自动化批量生产能力的企业。
京城股份(600860.SH)子公司天海工业2021年推出具有完全自主知识产权的新一代车载储氢IV型瓶,已建成一条柔性化IV型瓶生产线。
国富氢能是国内较早开展IV型储氢瓶技术研发的企业之一,已经实现70MPa IV型储氢瓶的量产,并在2022年建成氢能装备产业基地二期IV型瓶产线,产能可达1万只。
碳纤维国产化已见成效,部分零部件仍依赖进口
Ⅳ型储氢瓶推广的另一大障碍在于其原材料、制造工艺、核心零部件尚未完全实现国产化。
碳纤维复合材料是储氢瓶成本的最主要构成部分,占比60%-80%。早期,高压储氢瓶用碳纤维采用的T700、T800碳纤维主要由日本东丽供应。近年来,随着国内企业中复神鹰(688295.SH)、光威复材(300699.SZ)、吉林化纤(000420.SZ)取得技术突破,国产高性能碳纤维产能、质量等方面均有了显著提升,打破了国外垄断。
其中,中复神鹰已建成国内首条具有自主知识产权的千吨级干喷湿纺碳纤维产业化生产线,掌握了T300级、T700级、T800级等碳纤维的千吨级技术和T1000级百吨级技术。光威复材今年2月接受投资者调研时称,公司T700S级/T800S级目前2000吨产能处于满产状态。
碳纤维复合材料的缠绕工艺也对Ⅳ型储氢瓶的制造过程起到关键作用。良好的缠绕工艺不仅能减少碳纤维的使用量,从而降低成本,还能有效增强复合材料的耐压能力,进而提升储氢瓶的整体性能和使用寿命。目前,国内厂商在缠绕设备的工作效率、设计精准度以及材料利用效率等方面,仍有待进一步提高和优化。
瓶口阀是储氢瓶的另一重要零部件,集成了TPRD、电磁阀、压力传感器、温度传感器等功能部件,起到密封、降压稳压、温度压力实时监测等作用。瓶口阀需要避免发生侵蚀氢脆,技术难度较高。Ⅳ型储氢瓶的可靠密封技术是决定其储氢安全的关键。
国内70MPa的Ⅳ型瓶所应用的瓶口阀目前以进口为主,主要供应商包括加拿大GFI、意大利OMB和美国Luxfer等公司,成本较高,为35MPa的Ⅲ型储氢瓶瓶口阀的3-5倍。国内瓶口阀厂商如未势能源、富瑞特装(300228.SZ)、江苏神通(002438.SZ)等正在开展Ⅳ型瓶瓶口阀相关研发,但设计、制造和测试方面与国外尚存差距,大部分处于送样阶段,未形成批量供应能力。
Ⅳ型储氢瓶的内胆通常采用高复合塑料材料,研发内胆材料和精进成型工艺是实现Ⅳ型储氢瓶国产化的技术挑战之一。在充注氢气时,为防止内胆材料受损,需将氢气冷却至-40℃,这要求内胆材料具备良好的低温力学性能以抵抗变硬和脆化。此外,内胆材料还需具备优异的阻隔性和低氢气渗透率,以防内胆失稳或屈服,确保气瓶的使用寿命和安全性。
当前国内Ⅳ型储氢瓶内胆材料主要由国外企业供应,包括日本宇部兴产、荷兰帝斯曼、美国杜邦(塞拉尼斯)、法国阿科玛等,成本较高,是下一阶段国产化突破的重点。
固态储氢大势所趋,镁基材料率先实现产业化
固态储氢具备储氢密度高、工作压力低、安全性能好等优势,是安全用氢的发展方向,近年来商业价值持续提升。固态储氢材料主要有储氢合金、纳米材料和石墨烯材料。其中,储氢合金在我国已进入商业化探索阶段,镁系、钛系、稀土系三类固态储氢材料技术路线前景被看好。
镁合金作为储氢介质具有多重优势,包括成本低廉、质量轻、体积小、循环使用寿命长、可回收等。镁合金的体积储氢密度能够达到110kg/m³,分别是常温常压下氢气密度的1191倍、70MPa高压储氢密度的2.7倍以及低温液态氢密度的1.5倍。此外,镁合金在储放过程中能去除氢气中的一氧化碳和硫化物等杂质,提高纯度。但是,镁合金吸收和释放氢气的速度较慢,放氢温度需要达到300℃左右,增加了成本。同时,镁或镁合金表面容易形成一层致密的氧化层,导致反应速率的降低。
钛基储氢材料中,钛铁、钛锰、钛镍等合金最为普遍,其优点是制备简单、价格便宜及吸放氢条件温和。钛合金在20℃左右的常温环境中就能释放氢气,平衡氢压大约为0.3MPa,非常接近实际工业应用的需求,成本较为经济。然而,钛系储氢材料难以激活,容易受到中毒影响,滞后效应也较为严重。
稀土储氢材料包括以镧系、钇系、镨系等稀土元素为主要成分的合金。这类材料优点包括储氢容量高(每克材料能够存储5%-7%的氢气)、吸放温度适中、速度迅速、容易激活、热稳定性和循环稳定性好等。但是,稀土储氢材料的生产成本较高,在吸氢和放氢过程中需要经历特定的温度和压力变化,这对相关设备的设计和制造提出了更高要求。
在几条路线中,镁基储氢材料技术路线率先进入了产业化阶段。氢枫能源与上海交通大学丁文江院士团队、云海金属与重庆大学潘复生院士团队均采用合作方式进行了相关开发与研究。
2023年4月,氢枫能源联合上海交通大学氢科学中心发布了第一代吨级镁基固态储运氢车(MH-100T),单车储氢量为高压气态储氢的3倍左右,实现了常温常压储氢。今年1月,氢枫能源与宝武镁业(002182.SZ)就镁基固态储氢业务签署了《上海氢枫能源技术有限公司与宝武镁业科技股份有限公司战略合作协议》。今年9月,江苏华镁时代全球首条百吨级镁基固态储氢材料生产线在我国投料试产一次性开车成功。
总体来看,固态储氢处于发展早期。有业内观点认为,虽然材料层面的研究已经取得进展,但想实现固态储氢的大范围市场推广,需要进一步的系统性构建,包括产品、设备乃至完整解决方案。此外,当前固态储氢装置的成本较高,预计随着产线规模的扩大和自动化程度的提高,成本有望大幅降低。
厦钨新能(688778.SH)拥有5000吨储氢合金生产能力,第三代车载贮氢合金材料已批量生产,AB2系列储氢材料技术实现了突破。
厚普股份(300471.SZ)在氢能产业链布局11年,主要从事天然气、氢气的加注业务。今年4月,公司对外表示已具备固态储氢产品设计和集成能力,其钒基固态储氢已有项目落地。
圣元环保(300867.SZ)布局了多种固态储氢材料,包括AB5型(稀土系)、AB2型(钛系)和AB型(铁钛系),并对其进行动力总成系统集成开发。
安泰科技(000969.SZ)持股的安泰创明有固态电池业务,主要包括固态储氢材料及燃料电池发电系统、超级多孔骨架炭等储能材料。今年4月,公司对外表示安泰创明的近室温固态储氢材料主要是以稀土镍基、钛锰基为主的固态金属材料,目前已经量产。
北方稀土(600111.SH)旗下的国家稀土功能材料创新中心牵头研发了全国首台套固态储氢系统示范装置,此后又推出了固态储氢装置的氢燃料叉车,标志着稀土系储氢材料在移动载具领域得到成功应用。
(本文来自第一财经)
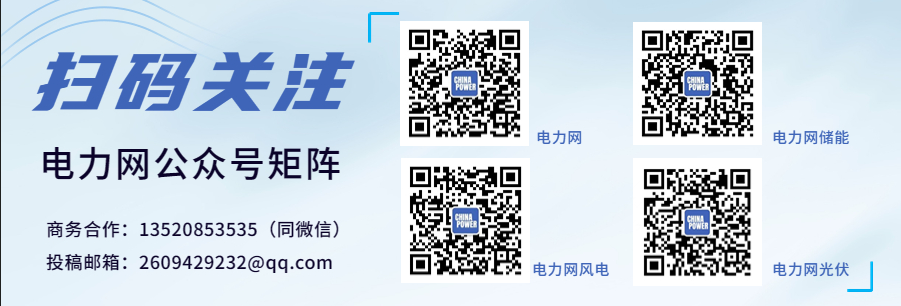
评论